With decades of experience in silicone raw materials, General Silicone (GS) can provide the best material formula according to the color and specifications required by customers, and provide customers with high-quality ready-to-use compounded materials for production through its professional compounding technology.
Provide Best Formula Design & Professional Compounding Technique
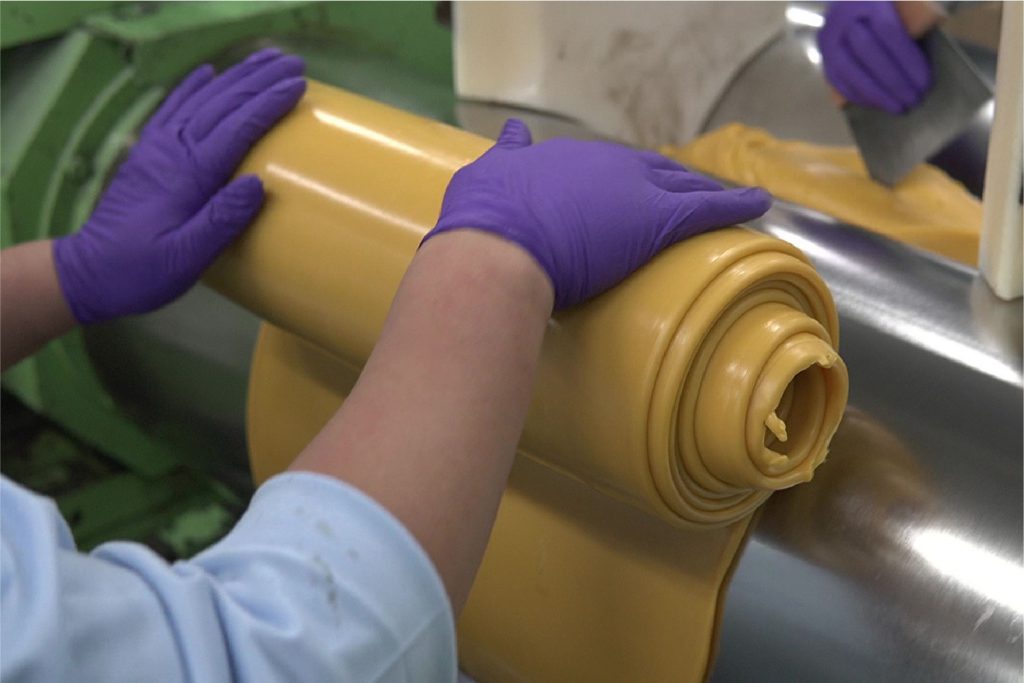
Keypad's Tactile Feel Design
One of important function for silicone keypad is to provide mechanical tactile feedback. Through extensive research and accumulated experience, GS is confident to meet the diverse demands of customers for the tactile feel of silicone keypad.
Electrical Switch Design
The key function of the silicone keypad is to provide electrical contact between the switch button and the PCB printed circuit board.
Tooling Design and Development
As the shrinkage rate of silicone is 3%-5%, special attention of the dimensional tolerances in tooling (mold) design is highly needed to control the shrinkage rate in order to comply with the M2 tolerance standard of ISO-3302. Also, because of the flexibility of the silicone resin and the tolerance of the tooling and fixtures/jigs to different factors, the special feature design must be employed in the tooling design in order to assemble properly.
Back-end Processing
Back-end processing includes silk screen printing, laser etching, spray coating, hard coating (epoxy coating), grinding, laminating, and die-cutting.